How much should the ability to manage the misalignment of a linear guide impact when designers and planners are faced with a new application project? The answer is a lot, particularly when the application to be realized does not require such rigorous precision as to impose the choice on a specific product, such as recirculating ball bearing guides.
In all other areas, the ability to manage misalignment is undoubtedly an advantage. Unmanaged misalignment, for example, is one of the leading causes of premature wear and tear on linear guides. Guides that theoretically should last for years end up not going beyond a few months if they are not aligned to the geometric tolerances necessary for smooth operation.
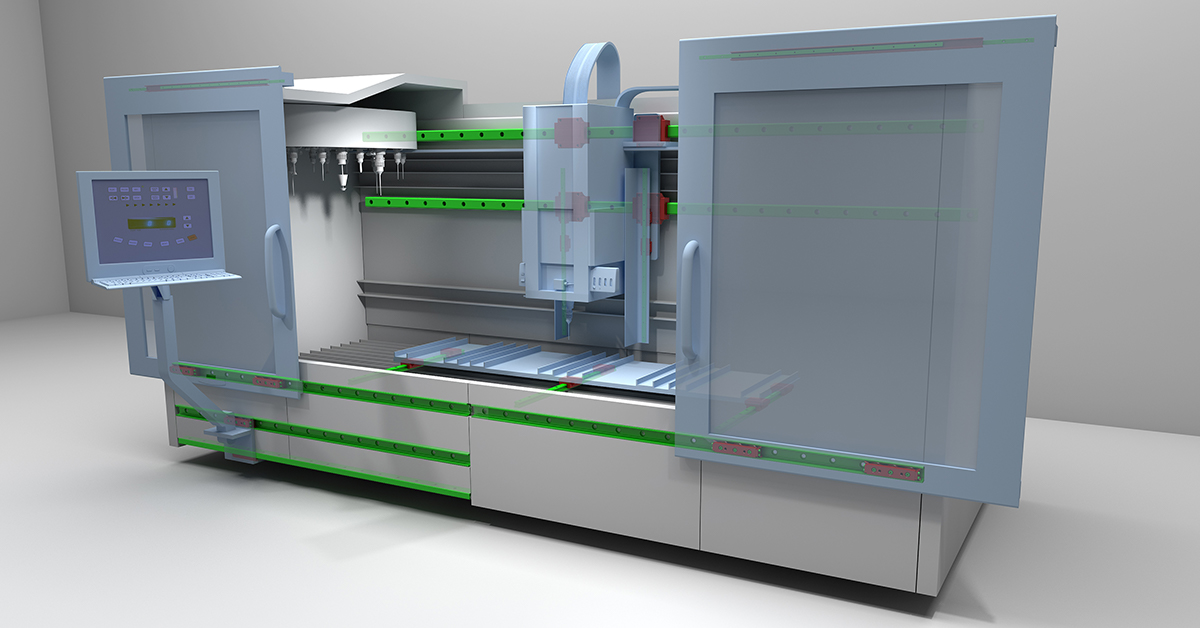
In addition to these aspects closely related to the operation of the application, there are also others, already in the design and preparation phase of the machine that will host the guides. Often the use of guides with little ability to self-align often requires constant rework and adjustments to the frames so that they are flat, straight or parallel enough to allow for smooth linear motion. Operations that lengthen the time needed to complete the machine and represent extra costs, often hidden in the initial phase, which increase the total cost of ownership of the new project.
Managing misalignment with the right linear guides
To avoid these repercussions, it is much better to manage the mismatch problem back at the beginning. Typically, there are two methods of doing this:
- Provide for the design and implementation of processes that completely eliminate misalignment
- Use linear guides capable of handling misalignment, such as Rollon's Compact Rail and Compact Rail Plus.
The design of solutions that eliminate misalignment at the origin, an option that in almost all cases involves the use of ball bearings, requires a high level of precision that, as mentioned earlier, "hides" a series of costs to adapt the mounting surfaces. In addition to the reworking and grinding mentioned above, it is often necessary to reinforce some parts of the guides in order to ensure a mounting surface that is sufficiently rigid to prevent flexing.
Other measures to counteract misalignment are also taken during assembly. Installers are often busy aligning rails millimeter by millimeter with painstaking precision, using ad hoc tools, fine adjustments and spacers.
The alternative, however, does exist and it is to use self-aligning bearing linear guides. In contrast to recirculating ball bearings, this type of guide has large rolling elements, profiles that allow for a certain amount of clearance and, finally, simple preload adjustment to allow for uniform load distribution across all bearings.

Why choose Rollon Compact Rail guides
Rollon's Compact Rail guides are an excellent example of misalignment-proof systems. Thanks to the unique geometry of the profiles, they are able to compensate for axial misalignment up to 3.9 mm and radial misalignment up to an angle of ±2°.

In practice, these capabilities translate into the ability to accept a guide height difference of 20 mm when the guide spacing is 500 mm. At the same time, the lateral translation capability of the rollers makes it possible to compensate for parallelism errors in the horizontal axis, i.e. when the guides converge or diverge.
For industrial machine builders, the advantages of using self-aligning guides translate into design freedom and cost reduction. If the condition of the guide mounting surface is not a critical factor, it is easier to design all or part of the machine frame with less expensive materials and manufacturing methods.
Compact Rail guides, for example, can be mounted directly to sheet metal, a surface that does not conform to the mounting of conventional linear guides. Doing so eliminates grinding of mounting surfaces and reliance on other complex assembly methods.
Want to know more about Compact Rail and the advantages it provides
