В авиастроении углепластик получил широкое распространение вследствие неустанного стремления производителей уменьшать массу и повышать топливную экономичность летательных аппаратов. Однако с технологической точки зрения процесс изготовления деталей из углепластика - особенно крупноразмерных деталей сложной конфигурации - весьма непрост, вследствие чего в некоторых случаях производителям даже приходится отказываться от этого материала в пользу иных, более простых в обработке композитных материалов, пусть даже и обладающих менее выигрышными сочетаниями весовых и прочностных характеристик.
В попытке предложить решение для этой проблемы, компанией «Criterion Manufacturing Solutions» была разработана для одного из заказчиков специальная установка термической формовки внутренних структурных деталей вертолётов из углепластика.
В конструкцию установки входит стол для изготовления многослойных структур, армированных углеродным волокном, методом ламинирования, причём на стол в процессе производства могут по командам оператора, в правильной последовательности и в заданной ориентации, подаваться до 150-ти нужным образом раскроенных листов из углеродного волокна.
Телескопическая направляющая: выигрышное решение
В процессе проектирования установки стало очевидно, что, с учётом размеров листов углеволокна, длины самого выполненного из стали и алюминия стола (составлявшей 7,5 м), а также с учётом габаритов насоса, от интегрируемой в установку системы линейного перемещения требовалось обеспечивать длины хода подвижных частей установки, превышающие один метр.
После переноса листов углеволокна на стол, рабочей частью станка обеспечивалось формование из них трубчатой детали, пропитанной специальными смолами, которые далее специальным образом полимеризовывались под воздействием высокой температуры и давления для получения углепластиковой трубчатой структурной детали вертолёта.
При этом как материалом, так и подвижными частями установки должны были совершаться достаточно сложные перемещения, для реализации которых проектировщикам требовалось разрешить целый ряд технических проблем:
• обеспечение работы установки с грузом, масса которого превышает одну тонну;
• обеспечение работы с консольно нависающими грузами, способными, в верхней половине стола, выходить за пределы последнего на 40 см;
• необходимость гарантировать точную повторяемость перемещений листов углеродного волокна и формуемой детали.
В результате было принято решение использовать в качестве основы для создания искомой системы линейного перемещения направляющие серии «Telescopic Rail» компании «Rollon».
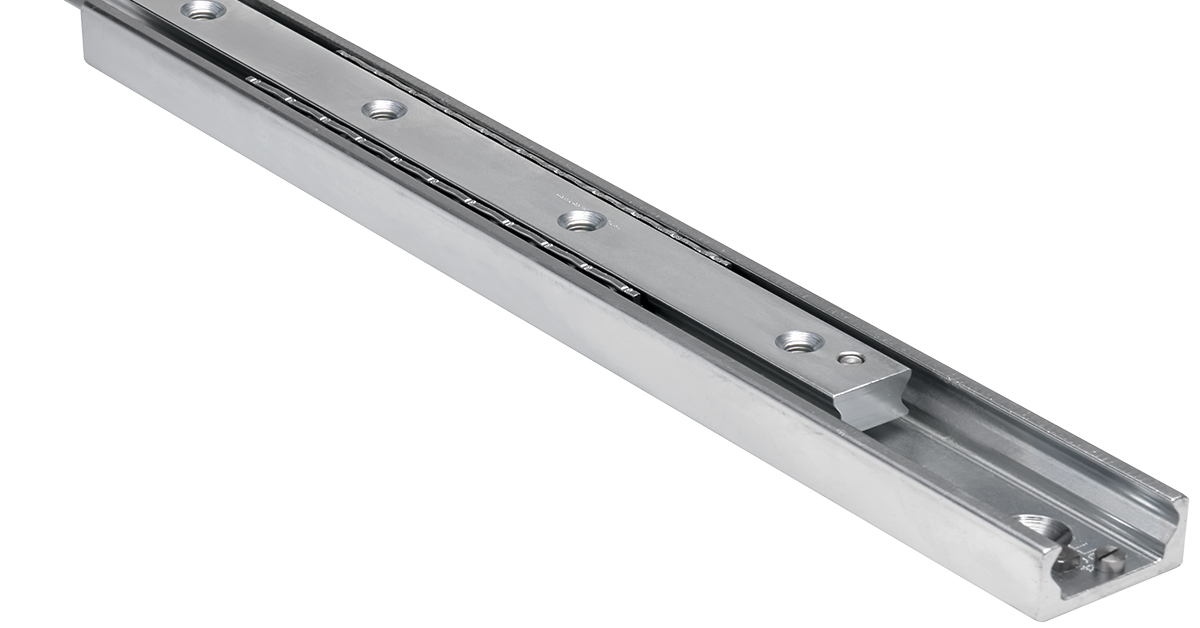
Все преимущества направляющих серии «Telescopic Rail»
Они позволили надлежащим образом - т.е. с соблюдением всех требований по грузоподъёмности, а также по повторяемости и точности перемещений - обеспечить перемещения и материала, и стола установки, и её вакуумного насоса.
Это стало возможным благодаря наличию у направляющих этой серии следующих технических преимуществ:
1. высокая грузоподъёмность.
Изделия данной серии изготовлены из холоднотянутой стали, и имеют закалённые индукционным методом и шлифованные направляющие, грузоподъёмность которых может достигать 3800 кг;
2. минимальный прогиб под нагрузкой.
Применение в конструкции направляющих «Telescopic Rail» усиленных профилей, отличающихся высокой механической жёсткостью, позволило свести прогиб под нагрузкой к минимуму;
3. большие длины хода.
Направляющие «Telescopic Rail» способны выдвигаться на длину, составляющую 150% от их длины в закрытом состоянии. Они доступны в вариантах полного и частичного выдвижения, а также, по особому запросу, могут поставляться с длиной хода, точно соответствующей техзаданию заказчика;
4. плавный безлюфтовый ход даже при работе с максимальной нагрузкой в круглосуточном режиме и без выходных;
5. длительный срок службы.
Наличие у дорожек качения индукционной закалки позволило улучшить долговечность направляющих.
В итоге, во многом благодаря оптимальному выбору телескопических направляющих от «Rollon», компании «Criterion Manufacturing Solutions» удалось создать установку для формовки углепластиковых деталей вертолётов, работающую с тяжёлыми консольно нависающими грузами и при этом отличающуюся высокой точностью перемещений её подвижных частей.
Реализовать подобное на базе традиционных телескопических направляющих было бы технически попросту невозможно.
А вот прочные направляющие «Telescopic Rail» с закалёнными дорожками качения справились даже с такой предельной нагрузкой, позволив проекту «взлететь».
Хотите узнать больше о телескопических направляющих, предлагаемых компанией «Rollon»? Скачайте каталог изделий!
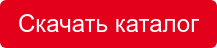